Introduction
Have you ever wondered where the energy from your engine goes when you’re stopped but still in drive (provided that your car isn’t manual)? Sure the wheels are stopped because the brakes are holding them in place, but the engine hasn’t stopped. Fuel is still being injected, the pistons are still going up and down, the crankshaft is still spinning, and the transmission is still connected to the engine because you aren’t in neutral.
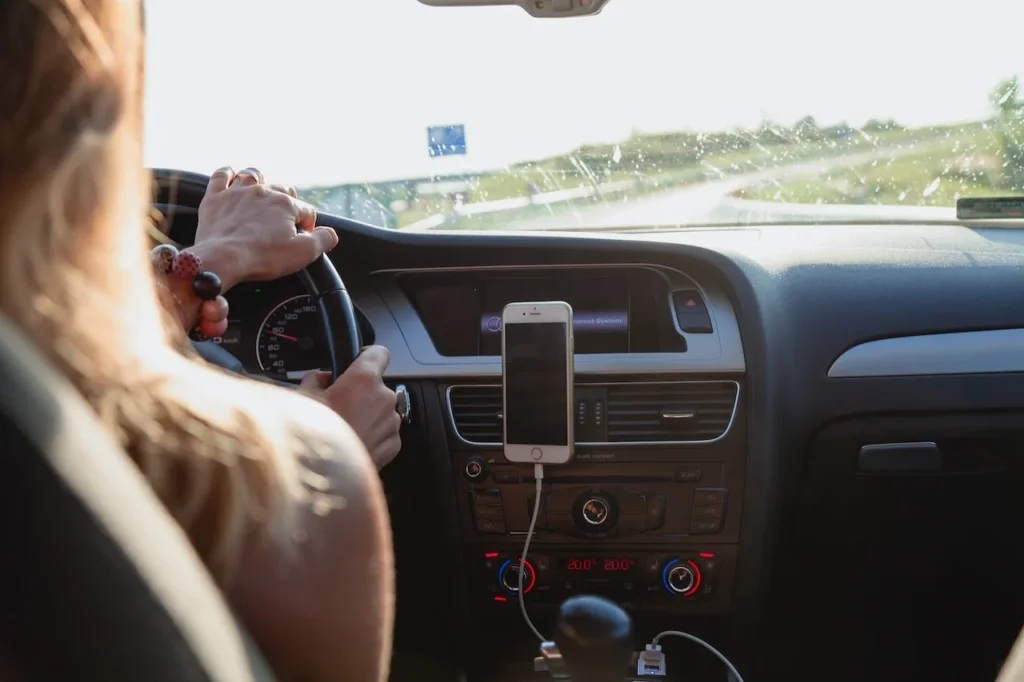
So then where is this energy going? Logically it would seem that the engine would have to stop spinning in order for the car to be still. The answer to this predicament lies within what’s called a Torque Converter.
What is a Torque Converter?
A Torque Converter is typically a part of an automatic transmission in a vehicle, though this is not always the case. For example, the Koenigsegg Regera has no transmission but does have a Torque Converter, but this is a topic for another article (read my article about the Koenigsegg One:1 here or watch the YouTube video here, which is another impressive car from Koenigsegg).
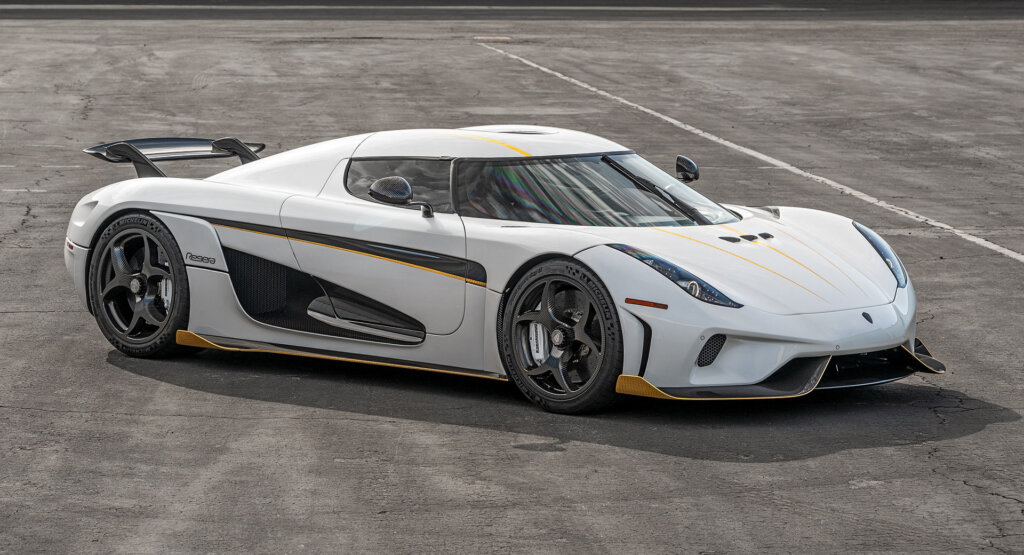
A Torque Converter has two main functions, the first is to keep the engine running while the car is stopped but in drive, and the second is to modulate how torque produced by the engine is transferred to the power train. It is essentially doing what the clutch would in a manual transmission for you, but it is an entirely mechanical part.
A Torque Converter is usually made up of 3 main parts, the first is an impellor (sometimes called the pump), the second is the stator (sometimes called the reactor) and the third is the turbine. The impellor is connected to the engine and spins with the engine as well, the turbine is connected to the transmission and spins when the transmission spins, and the stator is located between the impellor and turbine but is connected to neither of them. The turbine and impellor come together to form a sort of shell that all 3 parts reside within. And this shell is filled with transmission fluid.
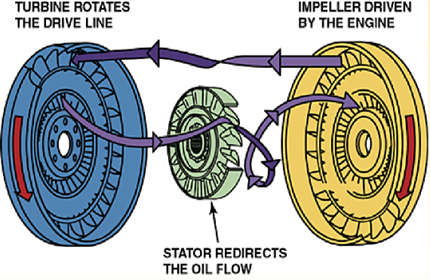
When the vehicle is stopped, the Torque Converter allows for the engine to essentially be disconnected from the transmission. At lower speeds the Torque Converter multiplies to torque produced by the engine to give the car more power to get it going and then stops multiplying the torque at higher speeds when this extra power is no longer needed. Now you may be asking how does it do all this? Read on into the next section to find out.
How do Torque Converters Work?
Before progressing, I would like to make it clear that this section aims only to provide a high-level overview of how a Torque Converter works. I will not be putting on an Engineering level masterclass in the subject, I am simply aiming to give you a general understanding.
The easiest way to visualize a Torque Converter is to imagine two halves of a shell coming together, one half of the shell contains the impellor, the other the turbine and the stator is located between them. The entire shell is filled with a fluid, this fluid is typically transmission fluid. The turbine and impellor both are metal wheels with fins on them that allow the fluid to spin them. The stator is considerably smaller than the turbine and impellor but also has fins on it and is constructed in a similar manner.
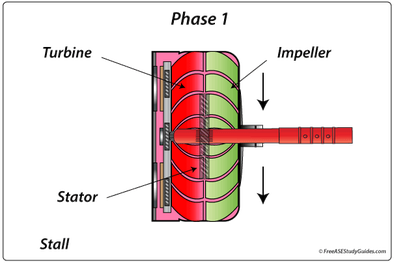
Now when the engine is spinning, the impellor will also be spinning. This will create a current in the fluid that flows within the shell, or Torque Converter. This current in the fluid will then turn the turbine, which will allow for the transmission to turn and hence the wheels. You can also picture it as two fans stacked in front of each other. The first fan will receive power from the wall and spin (this is the impellor receiving power from the engine), which will blow air at the second fan and cause it to spin even though it’s not plugged in (this is the turbine, and the fluid in this case is air). Now when the brakes are applied and the wheels are not moving, the pressure from the brakes will force the turbine to stay in place despite of the current. Therefore, allowing the engine to continue spinning while the vehicle is stopped but still in drive.
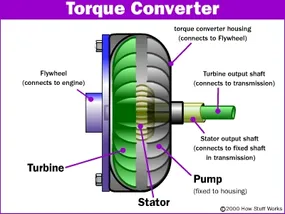
I would like to make a comparison/contrast with manual vehicles here as well. In a manual transmission the clutch is engaged by the driver, and the driver modulates the connection between the transmission and the engine. When the car is coming to a stop but still in gear, the clutch must be “let out” so it is no longer in contact with the engine, which disconnects the engine from the transmission. If the driver were to bring the car to a stop in gear without “letting out” the clutch, the engine would stall because the engine would be trying to rotate, but the brakes are holding the wheels and transmission in place. Since the clutch was not disconnected from the engine by the driver, the transmission and engine are still connected. Of course, this could all be avoided if the driver shifted the car into neutral before coming to a complete stop, which is typically done. The point I am trying to make with this statement is that in an automatic transmission the Torque Converter is performing the job of the clutch automatically.
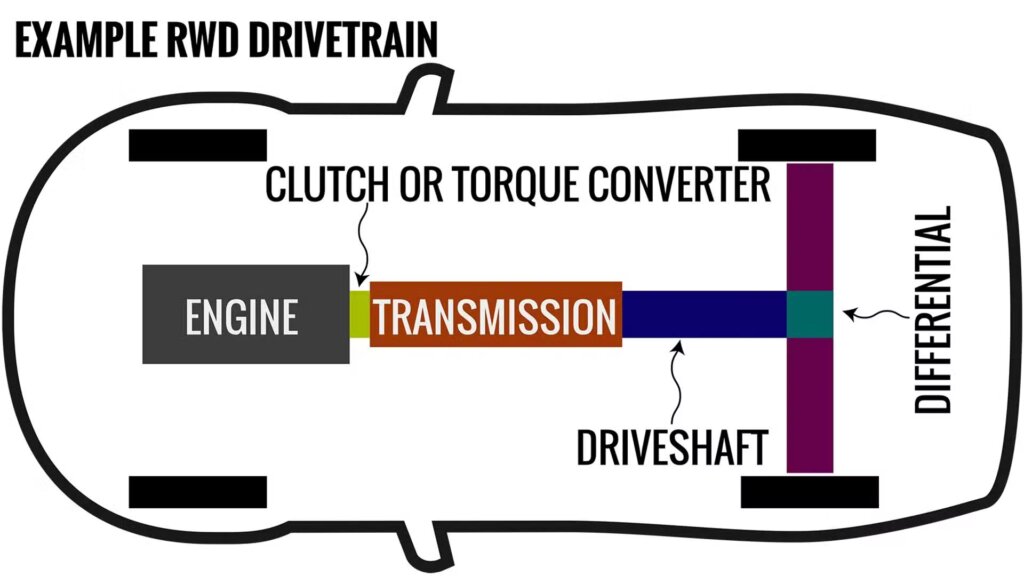
The second function of the Torque Converter is to modulate the torque delivery from the engine to the transmission. At lower speeds, typically when the vehicle is getting going from a dead stop, the Torque Converter multiplies the torque produced by the engine to get the vehicle moving quicker. At higher speeds, the Torque Converter smoothly transfers the torque generated by the engine as the extra torque is not needed if the car is already moving. It achieves this feat through the stator. The stator can only spin in a single direction and therefore can only affect the flow/current of the fluid in specific ways. At lower speeds, the stator remains fixed in place, and its fins redirect the flow of the fluid which increases the current, which increases the force that spins the turbine, and multiplies the torque produced by the engine. At higher speeds the stator rotates with the current, not aiming to have any impact on the current at all, which transfers torque from the engine to the transmission smoothly.
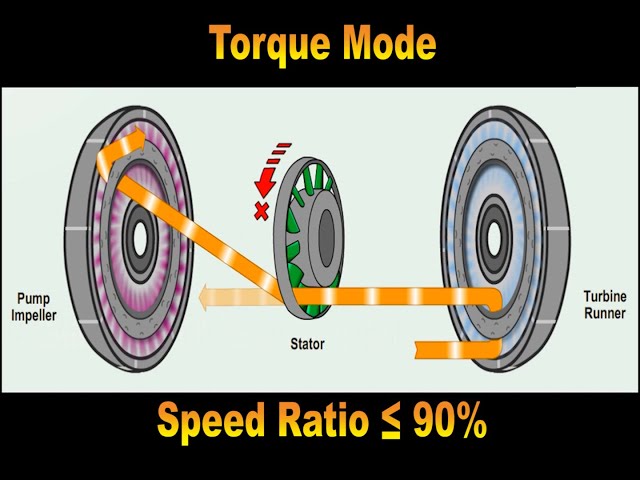
It is also worth noting that the transfer of torque from the engine to the transmission is not 100% efficient, some of it must be lost and this is commonly referred to as drivetrain loss. Some of the energy produced by the impellor will be lost to the fluid. The Torque Converter isn’t the only source of drivetrain power loss, but nonetheless it is worth a mention.
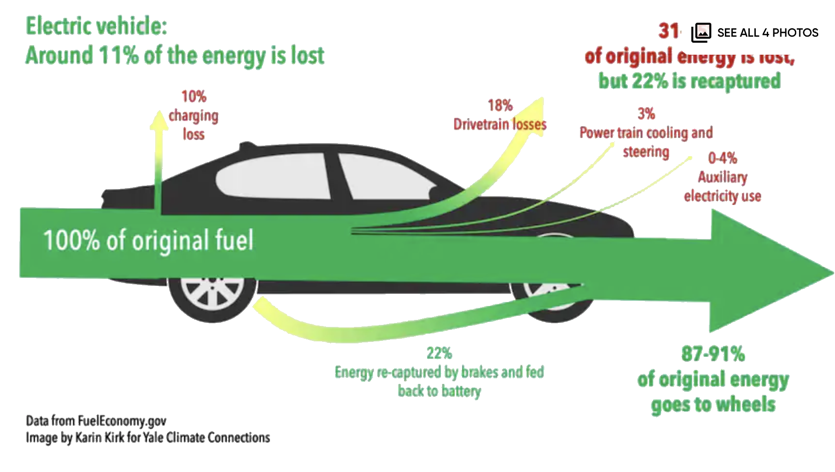
I would like to take a moment to restate that this is only a high-level overview and does not aim to provide an in-depth understanding by any means. I have left out many of the details to keep this explanation manageable and understandable for a broad audience. For example, although the impellor is connected to the engine, it sits of the part of the shell closer to the transmission, and the turbine sits of the half of the shell closer to the engine despite being connected to the engine. This is because a bearing needs to put between the turbine and crankshaft, and it is actually easier to do that if it is closer to the engine. But you can likely tell how including details like this would make this article much longer and less understandable.
Shameless Plug
On a final note, I’d like to make a shameless plug and recommend that you check out my YouTube channel here. I have several other videos published about my other articles, and a video about Torque Converters will be up soon (I’ll add a link here when the video is up). If you ever happen to find any of my articles hard to digest, I’d recommend the YouTube videos, they should be easier to follow (hopefully).
Sources: Donut, Sabin Civil Engineering, Putney’s, J.D. Power, Carscoops, EdTech Books, Free ASE Study Guides, Driveline Master, Auto | HowStuffWorks, Drive, Taycan Forum